A Bistro With A Bar
Deciding Was Easy
It was too easy to decide to remodel and build a bar. In late 2020 we negotiated a 20-year lease renewal, a long enough span to warrant sizable investment. We cut holes in the wall and pushed the Marketplace out of the wine bar into the shop next door. This final phase of incarnation had been sketched and contemplated for years, but the devil was in the details.
The restaurant is situated within a 20-foot tall cube, topped by a 14-inch thick “PT” concrete slab. When we remodeled the dining room in 2016 we framed a hard ceiling and created a mezzanine/attic above. At that time we ignored the suspended ceiling in the kitchen. The HVAC equipment had been suspended from the concrete lid in the cavernous interstitial space. The units were 20 years old and insufficient for keeping up with our robust spring and summer hot spells. I decided to replace the four worn out 3- and 4-ton units with three 5-ton split systems. These larger systems require economizers that meet the cooling load with outside air when it’s cool enough. This just makes sense and provide great savings, especially with the year-round cooling needs in the kitchen. There went $100,000!
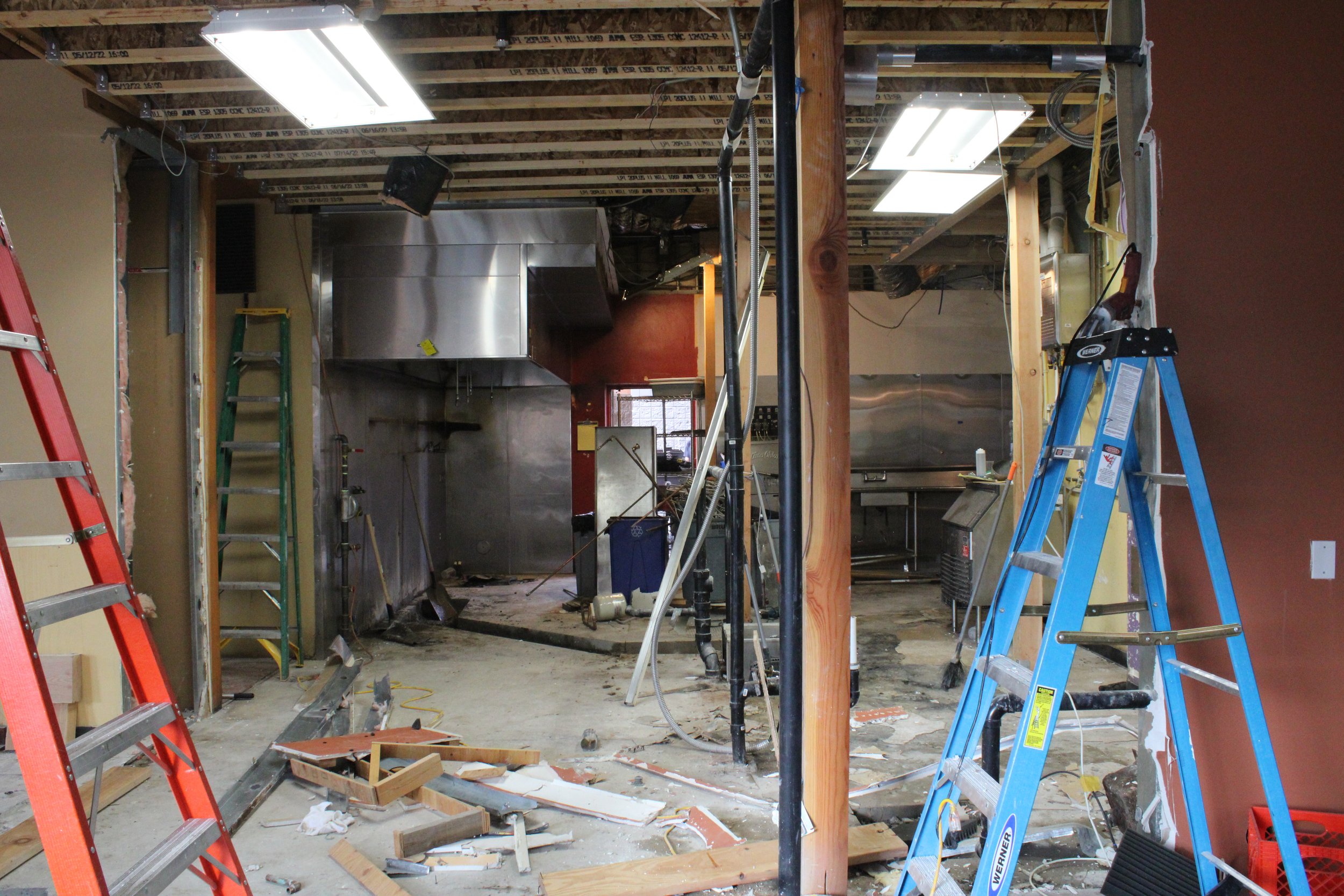
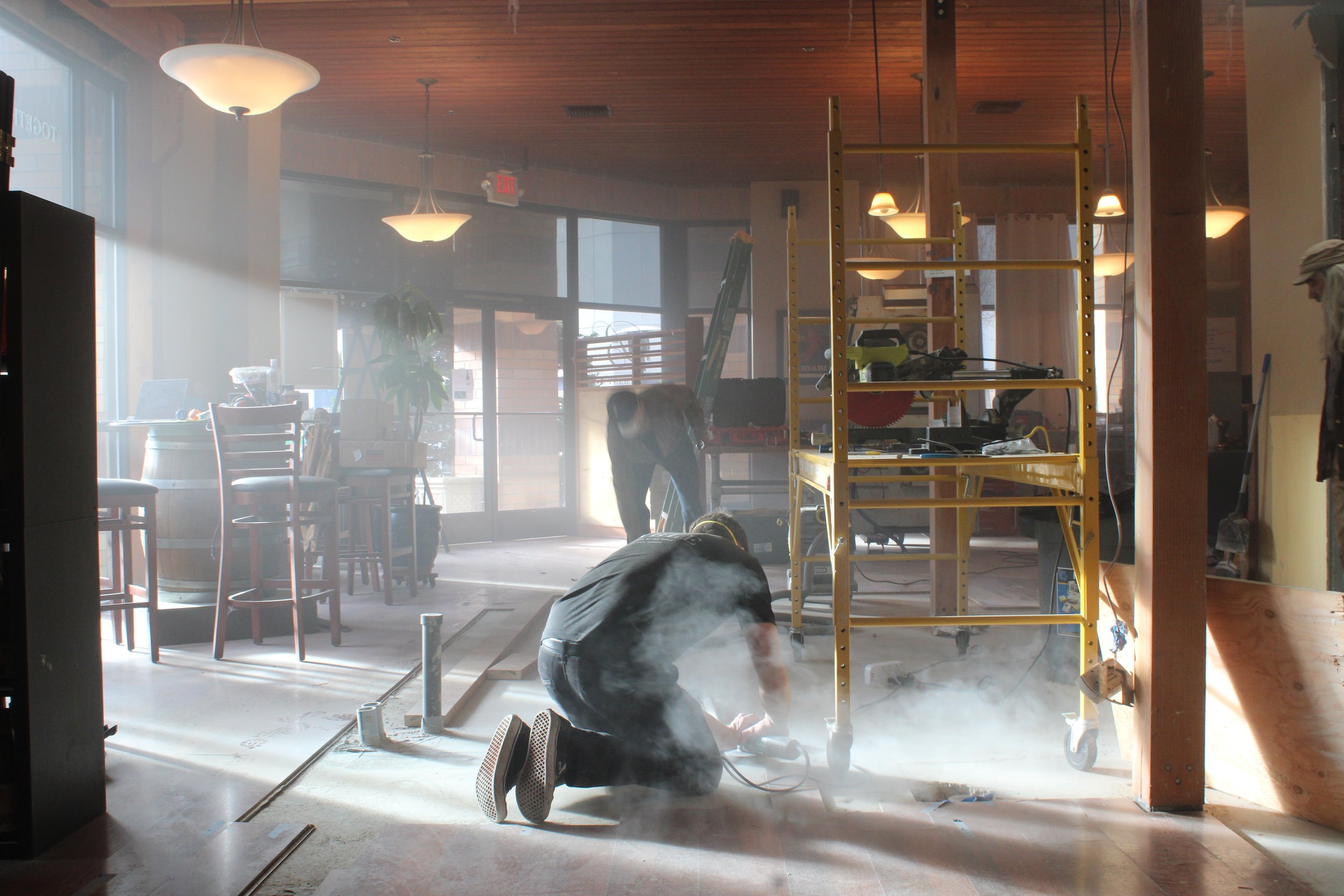
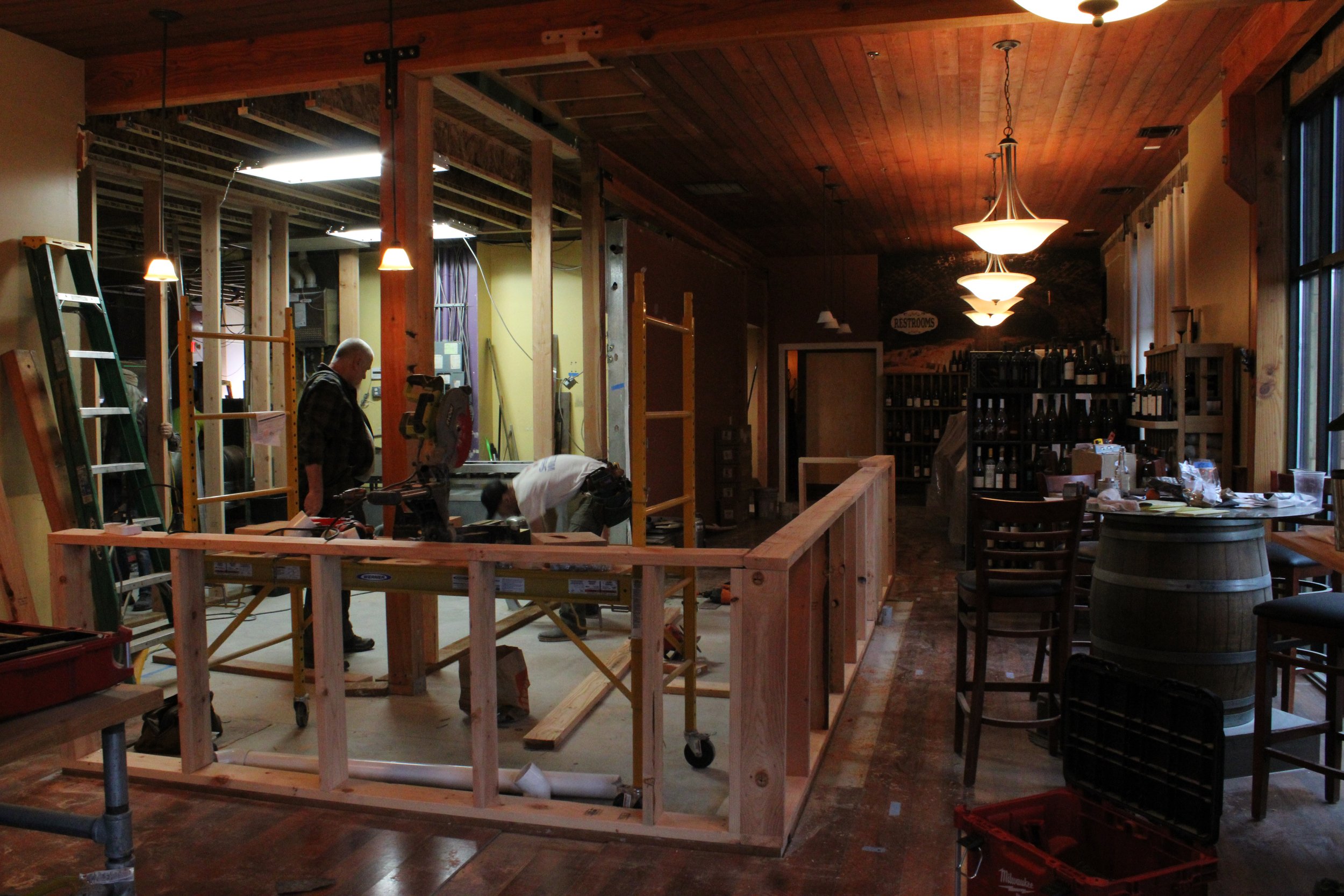

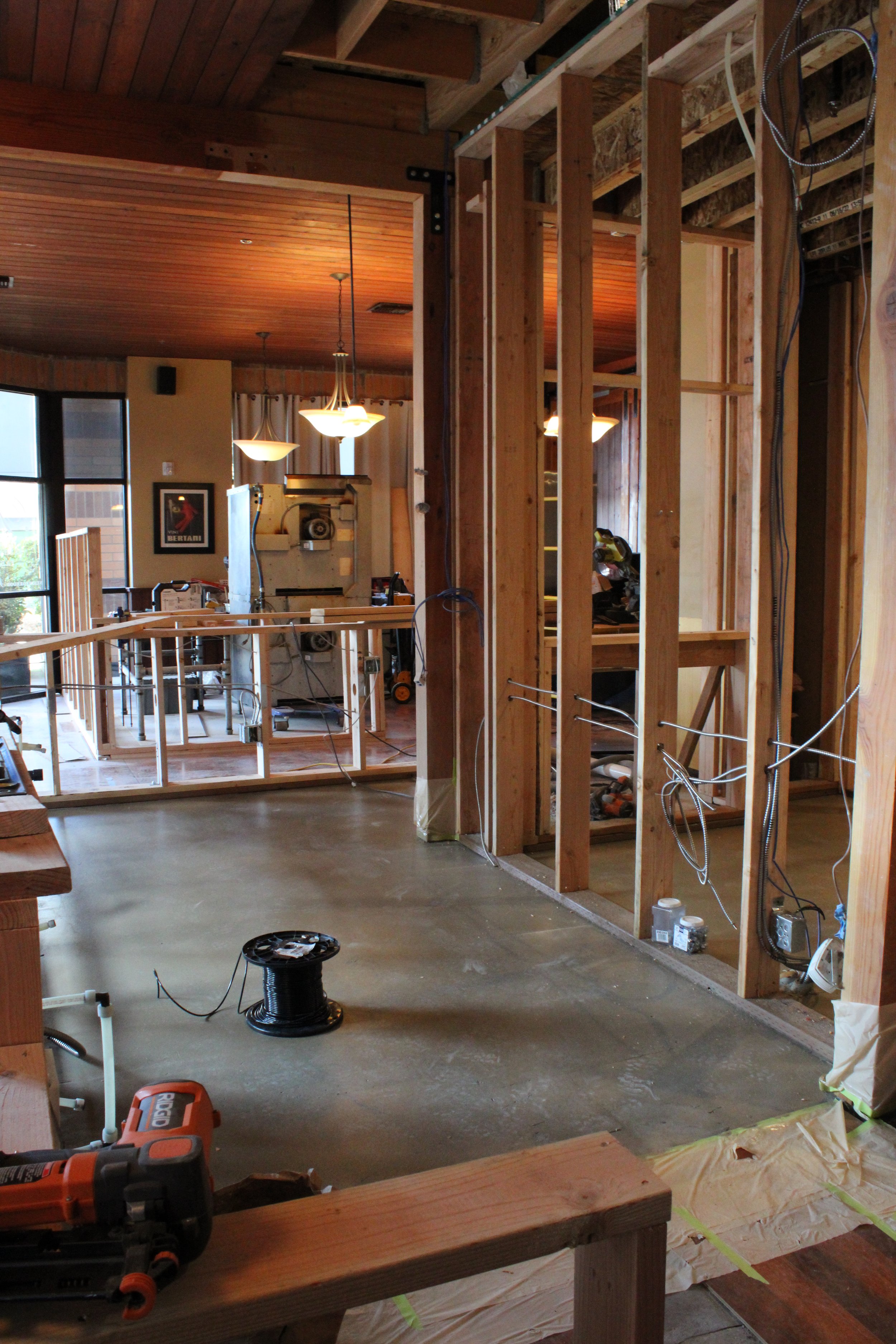
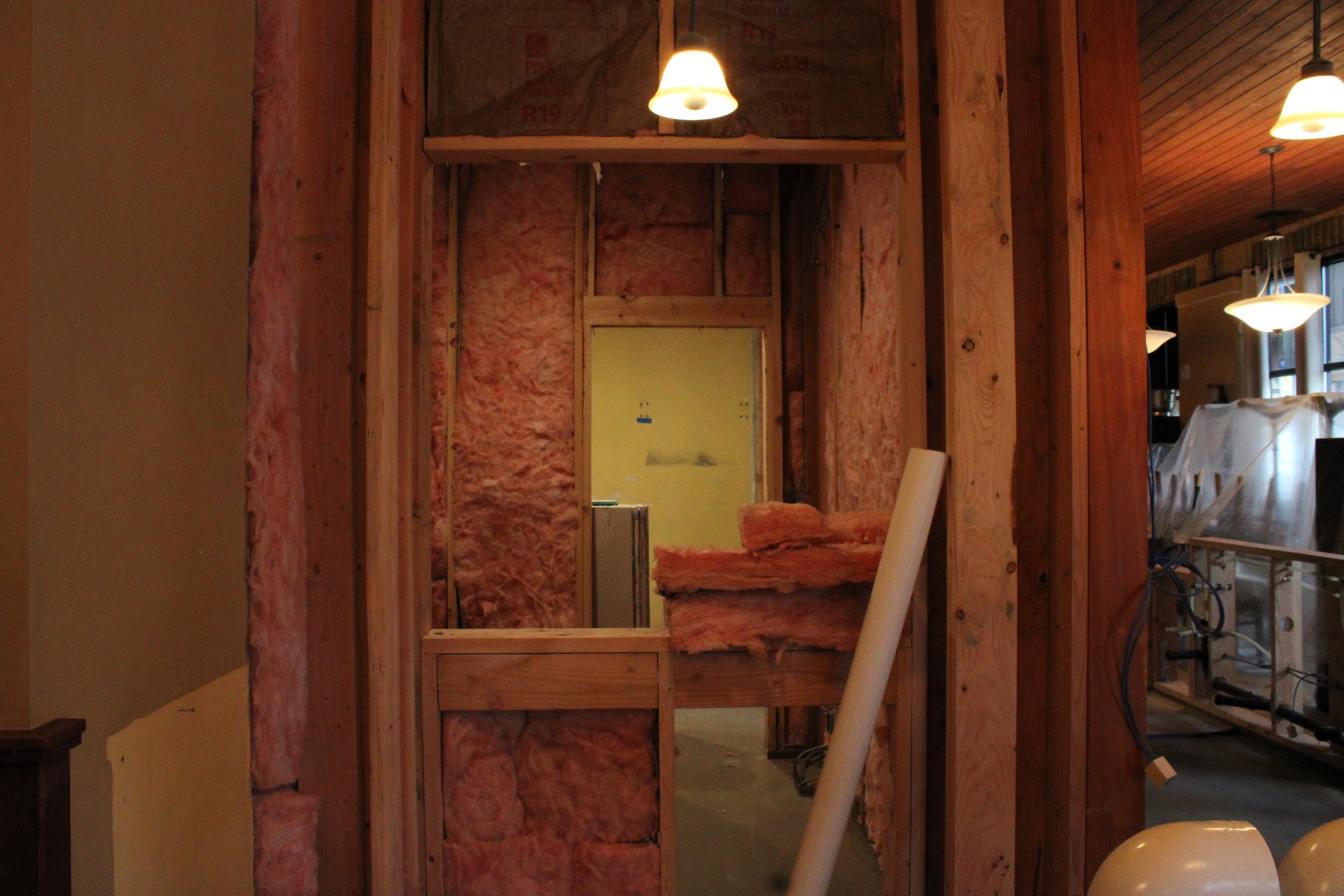
The building permit we eventually applied for specified “install new kitchen ceiling.” I would not get another chance to build something sturdy and usable so I exceeded all of the design requirements and built some of the sections to withstand loads as high as 100 pounds per square foot. Accessing an attic ten or eleven feet in the air is a bit dicey. The commercial pull-down stair cost over $3,000. The County managed to turn a 120-day plan review period into 210-day pig pile, so I split the project in two and built the ceiling in September. The permit was issued in October.
Stack-O-Walnut
Building a full bar, a wine cellar, a new dining room, gut-rehabbing the kitchen with new floors, relocated cooking line and dish pit plus replacing all the mechanical systems in five weeks was a pretty optimistic goal for January 2023. We ended up missing that target by three weeks and opened the first of March. I had set a budget of $300,000.
That we also missed by a mile. The final cost has surpassed $500,000. The schedule went into crisis when the building department inspection backlog grew to a week, then waits as long as ten days.
Pleading the case of a small business with two dozen out-of-work employees was sufficient to get much needed help from County supervisors who were able to pull the project from the flames, for which I am eternally grateful. Eventually the delays with inspections simply disguised the delays in building the bar, which was perilously behind schedule.
My son Adam is a woodworker and he took on the task of designing and building the bar. Janet suggested only that she wanted a classic look, reminiscent of an old Irish pub. My delays in completing the framing disabled Adam’s ability to measure for manufacturing. Meanwhile Adam, having just come off a major rehab project, was pulling long hours to complete the construction of his shop. This was to be a very large piece of furniture – one piece was 10’ x 13’. There was a convergence of delays that were all pulling to the same point. Adam broke the logjam when he showed up on site in a box truck loaded with giant pieces of walnut plywood glued up for the back bar. The bar top, four ten-foot slabs of walnut, was already on site climatizing.
Building A Classic Bar
I can nail things together and understand construction, but I wouldn’t call myself a carpenter. Adam is not just a carpenter, he is a woodworker, a craftsman. He is schooled in woodworking, but nobody teaches you how to build a bar, at least not this bar. After manufacturing most of the parts and pieces offsite, we began the framing. This wasn’t framing like I remember it. This was building a frame for a piece of furniture that had already been cut out. Spans as long as 13’ had to be perfectly square and plumb to within 1/32”! No fudging allowed!
For example, at one point, Adam realized the big arch had been hung 1/8” too low and was creating too much of a shadow line at the ceiling, so we pulled it and reinstalled it (perfectly square and plumb) all over again, 1/8” higher. I was known to wince from time to time but never stood in the way of his high standards. One fifteen-hour day after the other ticked by. Progress – perfection – did not come speedy. My suggestions that some of these time-consuming details could be eased up a bit were discarded; there might have been a hint of pity. Finally though I understood. I shut up and assumed my role as Apprentice #1. Carson, a uniquely able 18-year-old kitchen hand was Apprentice #2. Janet’s son Ryan was Apprentice #3. We sanded, held an end, fetched supplies, swept and vacuumed while Master – Adam – measured and remeasured.
Meanwhile the permit saga continued and, while progress was made, it consumed much energy and added stress. Realizing I was almost $200,000 over budget also added a special brand of stress. The final days a bar building were long. Construction continued during the two nights of our soft opening. Adam and I started at 6 AM and worked until dinner service, with the entire staff madly stashing tools and sweeping sawdust right up to the last moment. Adam returned after dinner and went back to work. I napped for three hours and joined him at 1 AM. We worked until 6 AM, went upstairs and slept until 8, then went down and worked all day. Still we were not able to put finish on the bar. Not that day and not the next. Finishing would have to wait for Sunday. I’d been dying to see it.
Walnut In All Its Beauty
Sunday was such a relief. We had the place to ourselves. The bar had been sanded with 220 grit paper but Adam decided it wasn’t good enough so he scraped the 30-foot-long bar with a cabinet scraper, cutting the final surface instead of grinding it. He fussed and fussed over the edge treatment and then executed the perfect solution. What a glorious moment it was when the oil was finally laid down. We were stunned by the beauty of it. Yet there was still so much to do
Getting Edgy
We finished building the shelves, installing and finishing the skirt around the bar and the back wall-panels. Layer after layer of finish is applied to the bar top, curing 12 hours between coats. First just rubbed on, then wet sanded with oil and 400-grit paper, then 600, then 600 again.
Staining & Curing
This is where I stand. As I write this I am not allowed to touch the bar. Adam came back after service and worked all night again. He’ll do the same tonight to lay down the final coat. During the day he is building a small cabinet, shelves and trim pieces to add the finishing touches. I am trying to muster the energy to tackle base and casing, paint and a half-million remaining details.
Nonetheless, we are open! Perfection is still a work in progress but I can see it from here. I need now to shift my focus to come up with another $100,000. Wish me luck!